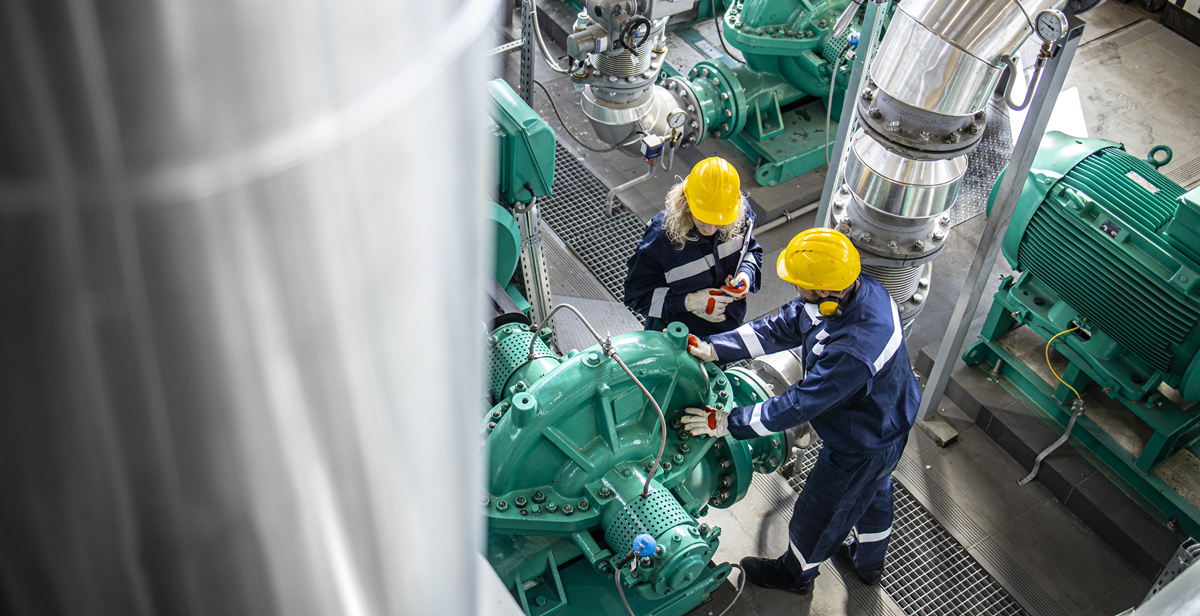
The manufacturing industry is facing an escalating challenge: a significant skills gap. With 600,000 positions currently unfilled and another 3.8 million jobs expected by 2033, the pressure is mounting on manufacturers to find and retain the skilled workforce necessary to meet the demands of a rapidly evolving industry.
One of the most pressing issues is the difficulty in finding qualified employees. Part of the challenge to attract talent are the distinct expectations younger workers bring to the workplace and the industry’s image problem.
Manufacturing jobs, despite offering competitive salaries and critical importance to society, often struggle to attract younger generations who are more inclined towards tech companies instead of traditional manufacturing jobs that they perceive as less hazardous and more aligned with modern, flexible work environments. This generational divide highlights the need for a broader rebranding of the industry to showcase its relevance and opportunities in today’s world.
This shortage is exacerbated by the fact that many current employees have outdated skills; up to 75% of workers in some companies are not equipped with the knowledge required for modern manufacturing environments. As companies grapple with these challenges, some are turning to automation to fill the void left by a shrinking workforce. However, automation won’t completely resolve the talent gap, as there will always be a need for humans to manage the systems to keep plants running.
Given these challenges, it’s imperative that manufacturers recognize that talent has become critical to business success— both the top and bottom lines. Companies must therefore take a strategic approach to investments in skills development, ensuring these initiatives are aligned with broader business goals and measured not just by the quality of learning but by the tangible outcomes they produce.
Strategic Steps to Address the Skills Gap
To effectively close the skills gap, manufacturers should focus on the following strategies:
- Tailored Skills Strategy: Develop customized training programs that address the specific needs of your workforce, ensuring that employees are equipped with the specific skills necessary for their roles.
- Employee Collaboration: Involve employees in the development of training programs. This not only empowers them but also aligns their career development with the company’s long-term objectives.
- Beyond Traditional Learning: Use advanced technologies to create immersive, flexible learning experiences that resonate with today’s workforce, moving beyond traditional classroom-based sessions and videos.
- Economic Evaluation of Investments: Training programs should be tied to a meaningful business case enabling leaders to measure outcomes. This ensures that investments in talent development contribute directly to the company’s overall success.
By implementing these strategies, manufacturers can not only boost proficiency, productivity, and job satisfaction among workers, but also enhance talent attraction and retention, ultimately minimizing recruitment costs.
How Voovio Can Help
Voovio’s Operational Excellence Platform helps leading manufacturing companies close their skills gap by onboarding operators more efficiently and building operator competency faster. Using digital replicas & immersive simulators operators can walk through the plant and practice critical procedures when, where and how they want to. This not only allows employees to engage in hands-on learning, aligning with today’s expectations but also enables trainers to track and measure outcomes effectively.
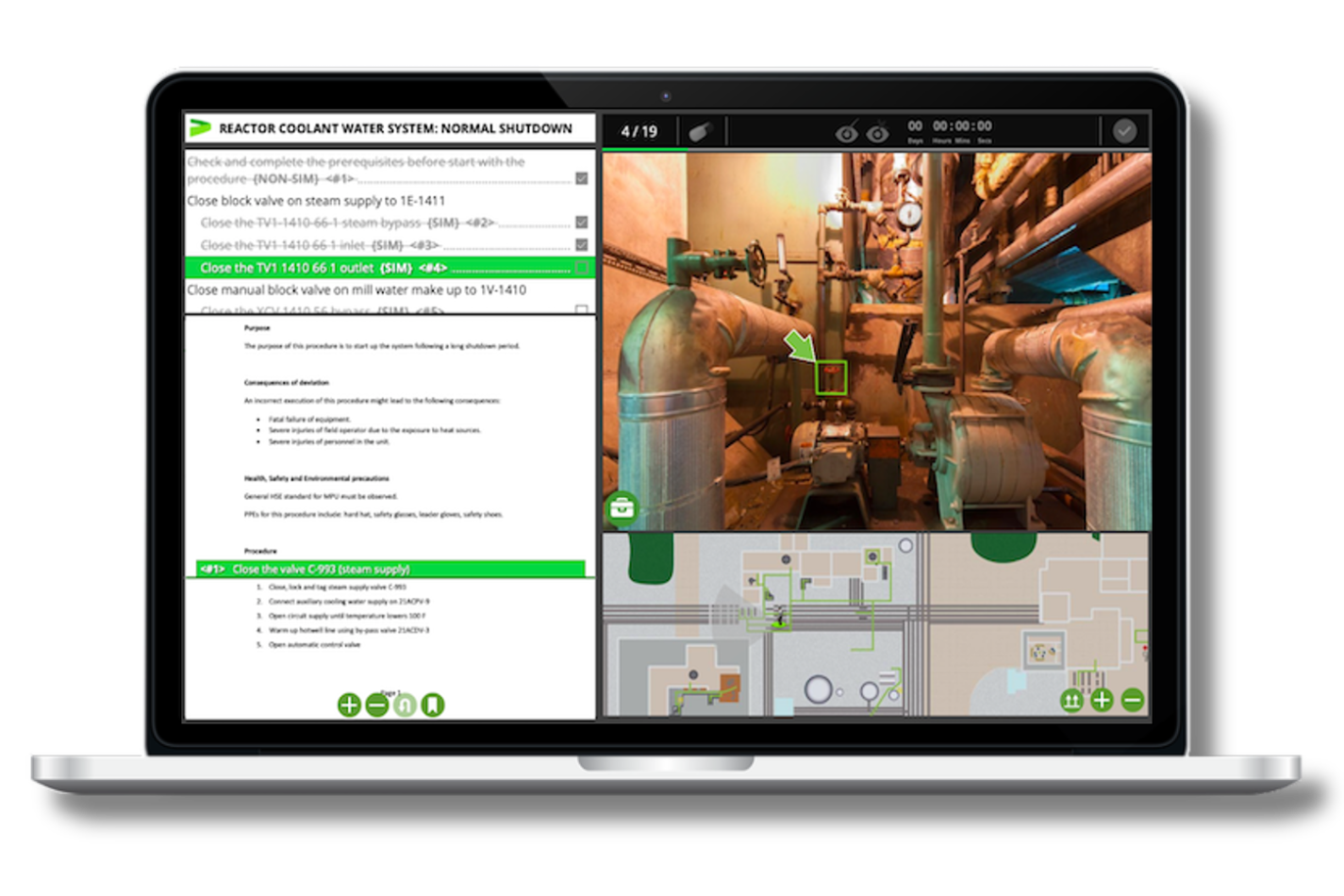
In conclusion, addressing the skills gap in manufacturing requires a technology-driven approach. Developing targeted training approaches and leveraging innovative tools will help manufacturers to have the skilled talent needed to thrive in an increasingly competitive and complex industry. Find out how Voovio can revolutionize your workforce training and help your company bridge the skills gap! Contact us here.
Sources