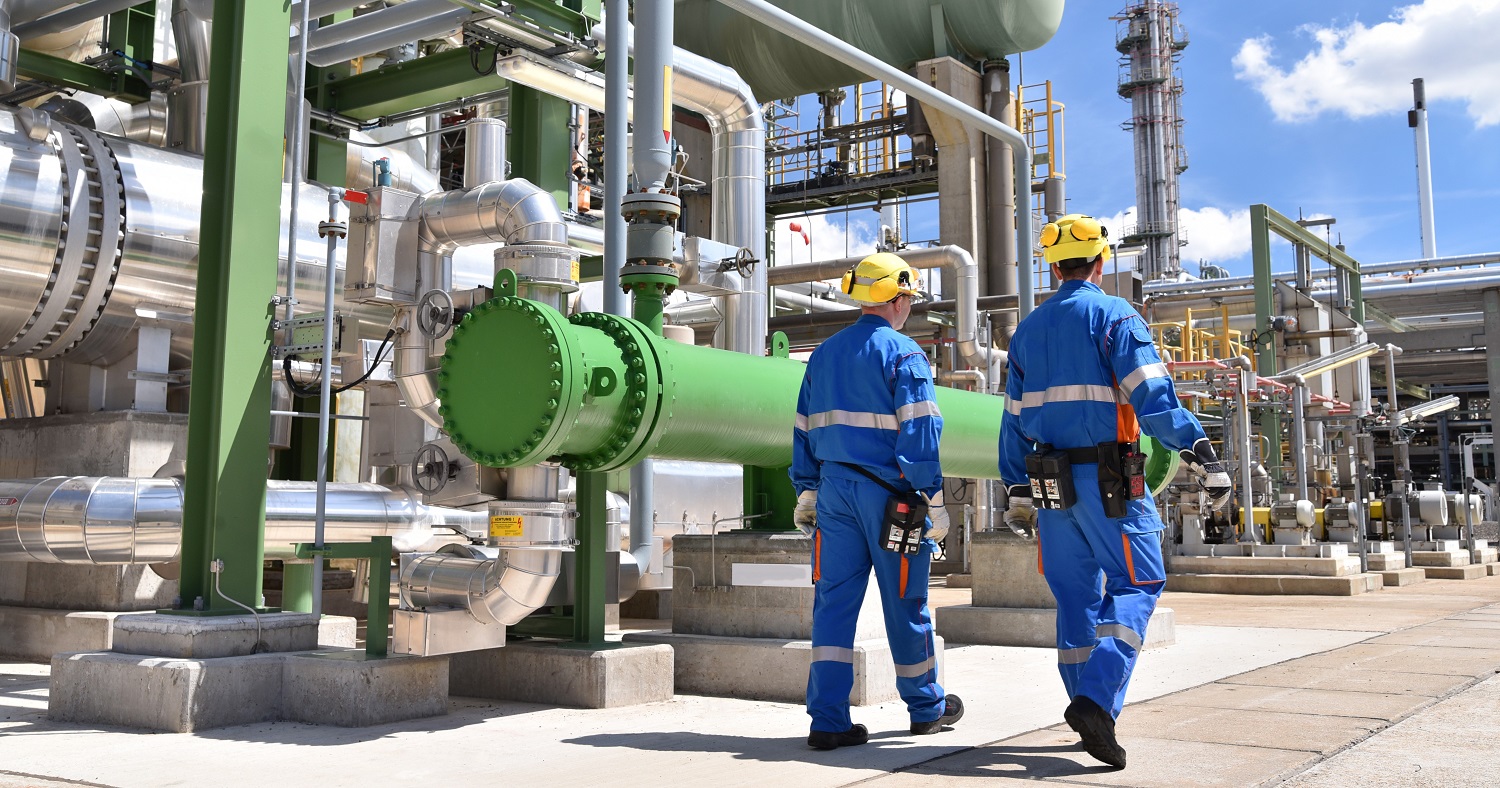
With a shifting workforce of experienced employees retiring and a decreasing pool of candidates starting work in plants, the significance of a well-trained and highly motivated workforce becomes more crucial than ever. However, numerous challenges impede the effectiveness of training programs in manufacturing. The 2024 Survey of Frontline Employee Training Programs sheds light on how training methods impact workforce performance in manufacturing.
The Challenges of Training Effectiveness
The survey asked industry leaders about their biggest challenges based on commonly reported challenges by training leaders in manufacturing.
Industry challenges
The top three challenges for companies include scheduling time for training (52%), having adequate resources (35%), and assessing training effectiveness (33%), see figure below. Further challenges also encompass making training engaging (32%), providing job-specific training, creating training content, documenting training and providing refresher training.
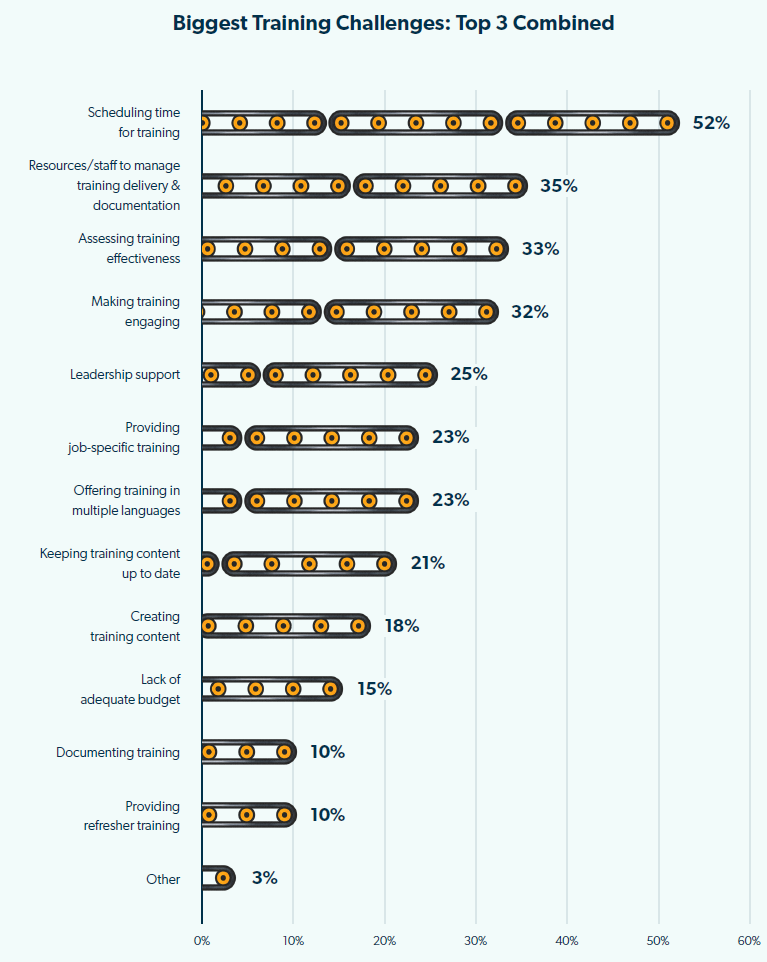
People challenges
What is more concerning are the challenges manufacturers shared in relation to their people. An alarming 73% of companies report that their employees do not consistently follow established protocols on the floor. The primary reasons are shown on the graph below and include learned bad habits, unengaged employees, and inadequate training from peers and supervisors.
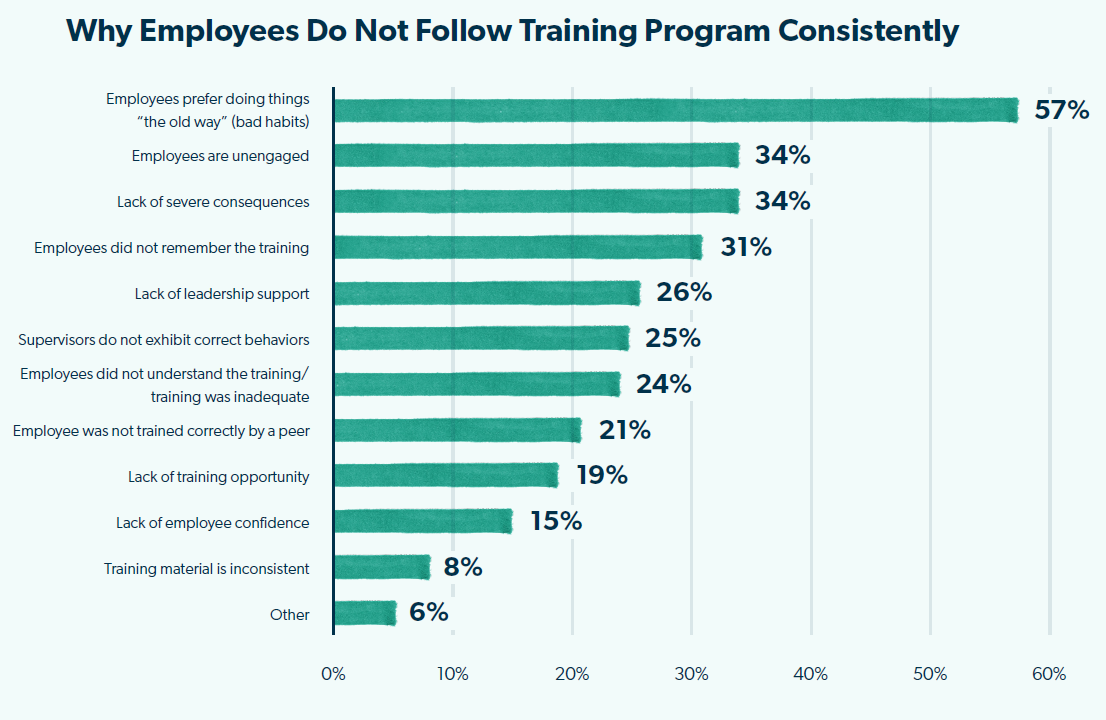
Misinformation
Another significant issue in the industry is the spread of misinformation among employees. About 21% of companies acknowledge that their employees pass along misinformation, followed by shortcuts, unsafe habits and operation risks. This issue is exacerbated by the reliance on peer-to-peer training, which takes place in 61% of facilities.
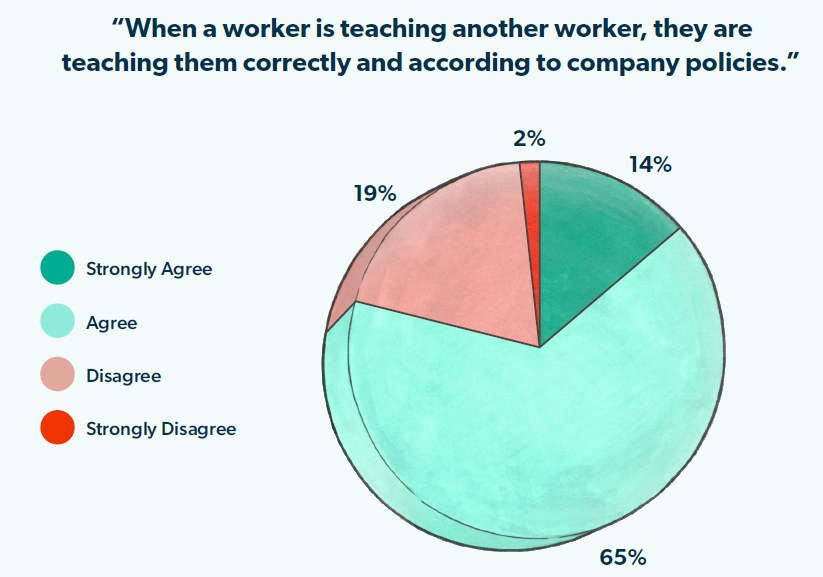
Best practices to overcome training challenges
But how can companies overcome these challenges, making their training more effective and keeping their employees engaged?
Implementing Site-Specific Training Materials
Using site-specific examples in training materials (photos, videos, etc.) can improve the employees’ ability to recognize and prevent problems. Companies that incorporate examples from their own facility into training score 91% on employee ability to recognize and prevent problems on the floor and are 88% more confident teaching each other correctly.

Have a strong system-based training program
It is clear that one-and-done training will not deliver the expected employee behaviors training intends. 94% of companies see positive return on investment (ROI) when their training program features strong, system-based and reinforcement/refresher process.
Utilizing Technology in Training
The report also stresses that leveraging eLearning and other technological tools can address many of the logistical challenges of traditional training methods. These tools facilitate consistent and accessible training for all employees, regardless of their location or shift. Industry leaders have confirmed this when deploying Voovio’s Digital Expert in their training programs. BASF, SABIC, Halliburton, Tesla, Suncor, Linde and many others use Voovio to tackle their frontline training challenges.
Traditional industry training relies heavily on paper manuals and peer-to-peer training, which can be inconsistent and unreliable. With personnel churn and retirements exacerbating the issue, Voovio addresses these challenges by capturing and institutionalizing critical undocumented SME knowledge through standardized training programs. This reduces reliance on SMEs and enhances the scarce field training opportunities, ensuring workforce competency.
Whereas eLearning is a standard learning form in most industries, in manufacturing most of it still happens on the floor, with peer-to-peer training. Less than half of manufacturers are utilizing eLearning to deliver training (47%) to frontline workers.
The organizations investing in training are the ones seeing the greatest ROI
The findings from the 2024 Survey of Frontline Employee Training Programs highlight the importance and impact of effective training in manufacturing.
“Organizations putting more time, more effort, and more money into their training programs are the same ones seeing the greatest return on their investment.” Strong training programs are 156% more likely to increase their budgets and see a positive ROI, with 98% of these companies confirming the benefits.
Implementing best practices such as site-specific training tools can drive success and ensure a well-trained, motivated workforce. Voovio’s Digital Expert builds and measures field competency, by providing an immersive digital replica of the plant. Providing 24/7 access to equipment specific knowhow, Voovio gives operators procedure clarity, standardizes training and reduces downtime.
Want to learn how this could help at your site? Request a demo here.