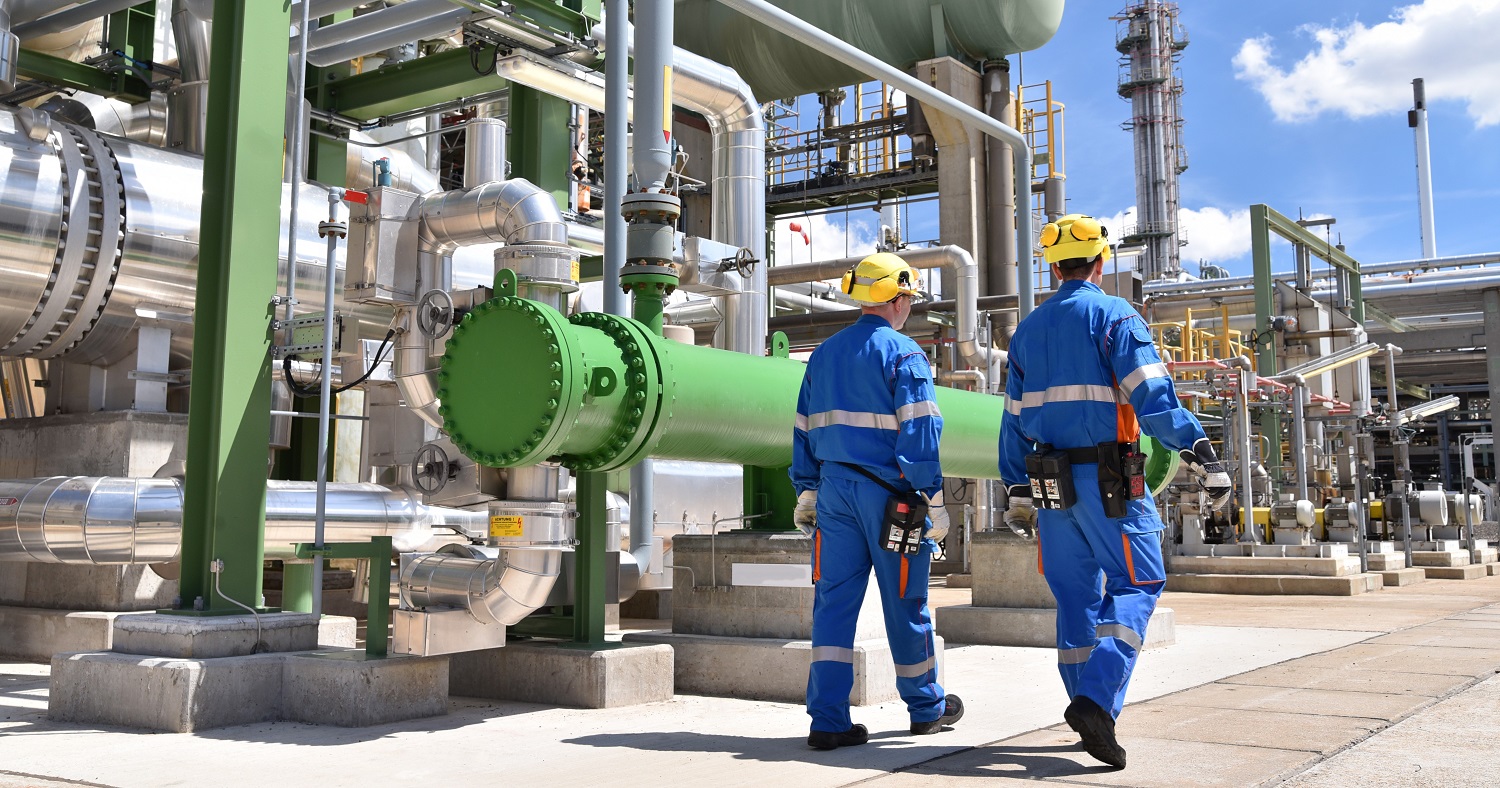
This German article was written by Dr. Susanna Voges, Director of Operations at Voovio for process industry professionals and was published in the in PROCESS on 1.30.2023. You can read the full article in PROCESS here.
Wenn ihr Anlagenfahrer Anfänger ist: Welche Chancen Onboarding 4.0 bietet
Chemische Produktionsanlagen zu fahren ist nichts für Anfänger. Ein falscher Handgriff und die Anlage steht. Doch die Zeiten in denen Anlagenfahrer 20 Jahre lang die gleiche Anlage bedienten sind vorbei. Und bald geht eine ganze Generation erfahrener Kräfte in Rente. Warum jetzt die richtige Zeit für eine neue Form des Onboarding ist.
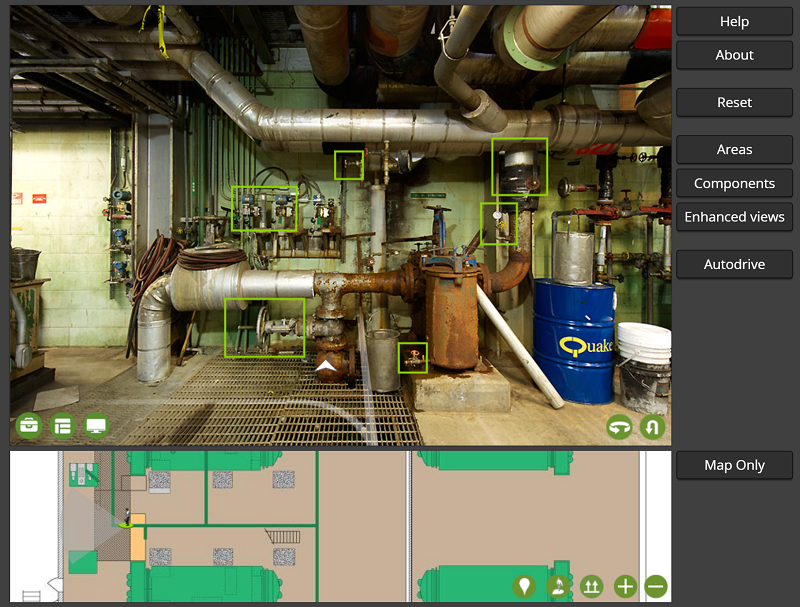
Das navigierbare, fotorealistische Abbild der Produktionsanlage (digitale Replika) funktioniert ohne VR-Brille.
Die Prozessindustrie misst dem Thema Automatisierung und Digitalisierung eine hohe Bedeutung für das Betreiben ihrer Produktionsanlagen bei. Kosteneinsparungen und Zuverlässigkeit sind die wesentlichen Treiber. Im Zuge der Digitalisierung mehren sich die Bemühungen, sich mithilfe von digitalen Zwillingen und künstlicher Intelligenz dem optimalen Betrieb der Anlagen noch weiter anzunähern – vor dem Hintergrund der Ressourceneffizienz und Wettbewerbsfähigkeit eine begrüßenswerte Entwicklung.
Nun lassen sich nicht alle manuellen Bedieneingriffe in Produktionsverfahren wirtschaftlich und technisch sinnvoll automatisieren. Auch vor dem Hintergrund möglicher Störszenarien sowie An- und Abfahrprozessen wird weiterhin gut ausgebildetes Bedienpersonal benötigt. Die Anforderungen an dieses Personal steigen tendenziell. So muss häufig eine größere Komplexität beherrscht und größere Arbeitsbereiche abgedeckt werden. Gleichzeitig sind hoch qualifizierte Chemikanten nicht leicht zu finden – wohl dem, der vorausschauend in ausreichender Menge selbst ausgebildet hat und seine Nachwuchstalente halten kann.
ERGÄNZENDES ZUM THEMA
Schlecht geschulte Quereinsteiger und die Folgen
Die Realität lässt Anlagenbetreibern allerdings häufig keine andere Wahl, als auf Quereinsteiger ohne vergleichbare fachliche Grundausbildung zurückzugreifen. Dies muss bei der anlagenspezifischen Qualifizierung angemessen berücksichtigt werden, was im betrieblichen Alltag oft schwer zu realisieren ist. Schon durch die hohe Zahl an Altersabgängen ist der Aufwand für die betriebliche Qualifizierung neuer Mitarbeiter um ein Vielfaches gestiegen. Meister und erfahrene Fachpaten reiben sich an verschiedenen Fronten auf – schließlich sind sie es, die ihr Wissen und ihre Erfahrung ebenfalls in die Weiterentwicklung der Produktionsanlagen einbringen sollen und wollen.
Die Folgen sind vielfältig und variieren je nach Situation des Betriebs. Es kommt zu ungeplanten Anlagenstillständen aus Personalmangel – nicht unbedingt weil generell zu wenig Personal da wäre, sondern weil Personal mit den spezifischen Kenntnissen für das Bedienen jener Anlage fehlt. Neue Mitarbeiter fühlen sich allein gelassen und überfordert. Eine unzureichende betriebliche Einarbeitung führt nicht zuletzt auch zu einer Häufung von Bedienfehlern, welche wiederum Umwelt- und Gesundheitsrisiken sowie ungeplante Anlagenausfälle und kostspielige Reparaturen nach sich ziehen können.
Die durch Opex-Maßnahmen und beispielsweise die Einführung verbesserter Instandhaltungskonzepte erreichten Verbesserungen können so leicht zunichte gemacht werden.
Onboarding 4.0 mit Enhanced Reality (ER)
Warum also nicht die Vorzüge digitaler Innovationen auch im Bereich der betrieblichen Qualifizierung einsetzen? Gartner Research (Emerging Technologies: Revenue Opportunity Projection of Digital Twins) bezeichnet in seiner Studie von 1922 den Ansatz als „Digital Twin of The Person“. Anders als ein digitaler Zwilling im herkömmlichen Sinne setzt dieser an der Person an, welche mit der Produktionsanlage interagiert – mit der Intention, den Menschen bei dieser Arbeit zu unterstützen. Meist kommen für derartige Werkzeuge Virtual-Reality-Systeme zum Einsatz, welche auf 3D-Modellen basieren. Die wichtigsten Limitierungen solcher Werkzeuge sind der Aufwand für die betriebliche Implementierung und die Umsetzung von Anlagenänderungen sowie die Notwendigkeit von empfindlicher und teurer Ausrüstung wie VR-Brillen.
Einen grundlegenden Vorteil bietet deshalb die von Voovio entwickelte patentierte Enhanced-Reality-(ER)-Technologie. Grundlage ist ein navigierbares digitales 3D-Abbild der Produktionsanlage (digitale Replika), welches aus 2D-Fotografien besteht. Dank dieser technologischen Grundlage ist die betriebliche Umsetzung deutlich einfacher. Das fotografische Material macht die Darstellungen zudem so realistisch, dass keine besondere Ausrüstung benötigt wird, um den für das Lernen so wichtigen Effekt der Immersion zu erzielen. Der Pragmatismus dieses Ansatzes prädestiniert ihn für die Anwendung im betrieblichen Umfeld.
Jeder kann sich das Wissen selbst erarbeiten
Auf die digitale Replika der Produktionsanlage aufbauend, werden Betriebsanweisungen (SOP) simuliert. Anhand dieser Simulationen kann der Mitarbeiter sich das praktische Wissen, wie die Anlage zu bedienen ist, Schritt für Schritt aneignen und sein Wissen anschließend überprüfen. Die Bedeutung für das Onboarding liegt auf der Hand: Der Mitarbeiter bekommt ein Werkzeug an die Seite, welches ihm erlaubt, unabhängig von Meistern oder Fachpaten und im eigenen Tempo, seine Kompetenzen auszubauen. Gleichzeitig werden eben die Meister und Paten entlastet. Der neue Mitarbeiter wird in die Lage versetzt, aufgrund der im Virtuellen erarbeiteten Grundlagen, stärker vom spezifischen Wissen seiner erfahrenen Kollegen und Vorgesetzten zu profitieren, da er qualifiziertere Fragen stellen kann.
Diese Vorteile der anlagenspezifischen Einarbeitung werden ergänzt durch klarere Arbeitsanweisungen und eine deutlich geringere Fehlerquote. Denn im Rahmen der betrieblichen Einführung der Enhanced-Reality-Plattform werden die zu simulierenden Betriebsanweisungen gemeinsam mit einem betrieblichen Experten Schritt für Schritt vor Ort durchgegangen und dabei das Fotomaterial für den Aufbau der Replika aufgenommen. Hierbei wird die, für die Simulation erforderliche, Eindeutigkeit generiert: Arbeitsabläufe müssen für die Digitalisierung präzise erfasst sein. Die Erfahrung zeigt, dass bestehende Betriebsanweisungen fast nie diesen Anforderungen genügen, da die Texte oft Vereinfachungen und Generalisierungen enthalten. Oft erhöht sich so die Zahl der Schritte der Betriebsanweisungen um etwa die Hälfte. Durch die so erzielte, präzisere Formulierung der Arbeitsanweisungen werden mögliche Ursachen für Bedienfehler eliminiert. Zudem profitieren Mitarbeiter, die nicht über die fachspezifische formale Qualifikation oder vergleichbare Erfahrung verfügen.
Die Praxis belegt den Erfolg
Gemäß einer Studie von Ron Moore (Making Common Sense Common Practice) aus dem Mai 2004 sind Fehler bei der Bedienung von Produktionsanlagen für etwa 23 Prozent der ungeplanten Anlagenausfälle verantwortlich und verursachen damit einen erheblichen wirtschaftlichen Schaden. Anhand konkreter Anwendungen kann gezeigt werden, dass die Fehlerquote mittels des ER-basierten Trainings deutlich reduziert werden kann. Beispielhaft sei hier ein Anwender im Bereich Raffinerie genannt, der eine hohe Fehlerquote beim Befüllen von Tankwagen durch Fremdfirmenmitarbeiter (Fahrer) beklagte. Diese Fehler verursachten Stillstände, kostspielige Reparaturen, Leckagen und zusätzliche Reinigungsarbeiten. Indem die Fahrer mittels einer, auf den Anwendungsfall adaptierten, ER-Plattform geschult wurden, konnten derartige Fehler in Folge vollständig vermieden werden. In einem anderen Fall – ebenfalls eine Raffinerie betreffend – führten Bedienfehler wiederkehrend zu meldepflichtigen Emissionen, welche neben immateriellem Schaden auch zu Strafzahlungen führte. Auch hier konnten mithilfe von ER-Training die durch Bedienfehler verursachten Umweltereignisse beseitigt werden.
Geschultes Personal ist ein Erfolgsfaktor
Für das erfolgreiche Betreiben von Produktionsanlagen in der chemischen und petrochemischen Industrie ist hervorragend geschultes Personal ein kritischer Erfolgsfaktor. Im Hinblick auf die anlagenspezifische Qualifikation liefern moderne, auf Visualisierung der Produktionsanlage basierende, Systeme einen essenziellen Beitrag, welcher vor dem Hintergrund der aktuellen Herausforderungen wie massiver personeller Fluktuation kaum zu überschätzen ist. In dieser Klasse der digitalen Trainingssimulatoren, ist die Enhanced-Reality-Technologie von Voovio hervorzuheben, die sowohl durch Pragmatismus als auch Realismus der Visualisierung hervorsticht. So ist ein hoch effektives, immersives Training auch ohne empfindliche und teure Hardware gewährleistet und die betriebliche Umsetzung kann leicht auf dem aktuellen Stand gehalten werden – eine Grundvoraussetzung für die nachhaltige Anwendung.
Quellen:
(1) https://www.gartner.com/en/documents/4011590
(2) https://patents.google.com/patent/US20120099804A1/en
(3) Ron Moore, “Making Common Sense Common Practice”, ISBN-13: 978-0750678216,ISBN-10: 0750678216, Butterworth-Heinemann; 3rd edition (May 21, 2004): Making Common Sense Common Practice | ScienceDirect
Über die Autorin
Dr. Susanna Voges ist Director of Operations bei Voovio. Mit 15 Jahren Erfahrung in der Prozessindustrie, kennt Susanna Voges die Herausforderungen chemischer Betriebe aus erster Hand. Einen Großteil ihrer Karriere verbrachte sie als Werksleiterin bei BASF in Ludwigshafen und später bei Sun Chemical in Ludwigshafen. Um Susanna zu kontaktieren, senden Sie bitte eine E-Mail an svoges@voovio.com.