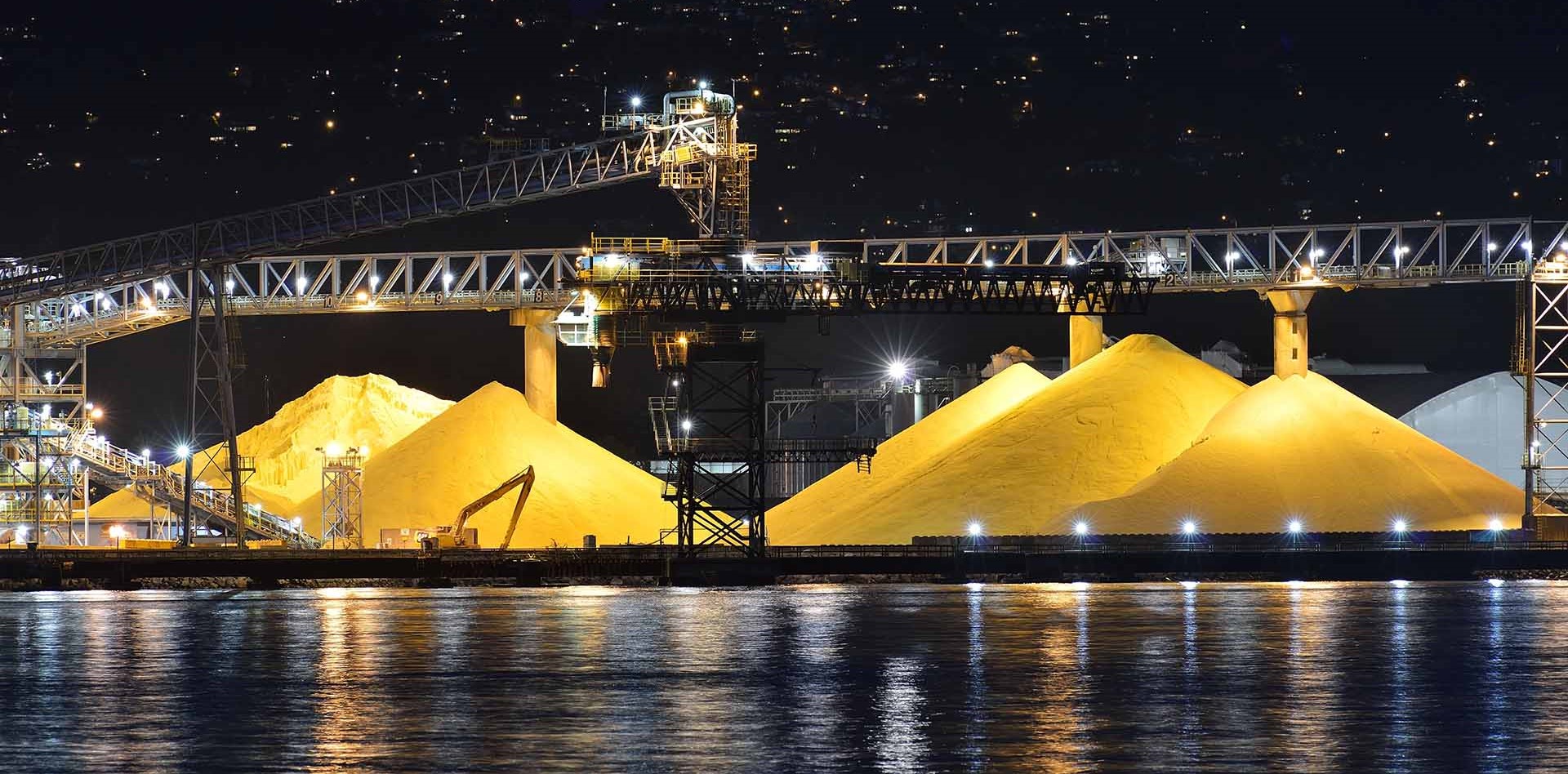
There is a growing skills gap in the sulphur industry due to the changing nature of the workforce. The traditional ways of doing things are no longer working effectively. Knowledge is lost with retiring subject matter experts (SMEs) and other experienced operations staff leaving a reducing pool of SMEs. In this article, published in the July-August 2023 issue of Sulphur magazine, a case study reviews how knowledge automation solved the skills gap in a sulphur recovery unit at a major US refinery.
According to Deloitte’s and The Manufacturing Institute’s report on the state of the industrial workforce, attracting and retaining a quality workforce is a top focus for 83% of manufacturers surveyed. This perfectly aligns with what is heard across plants in the US and abroad: The loss of experienced people in operating facilities. Plants are clinging on to baby boomers for as long as they can, fearing the ~30-40 years of equipment specific expertise will be lost forever. As manufacturing facilities expand, thanks to the strong growth of US manufacturing, companies fight to attract an increasingly smaller pool of candidates to run their plants. The workforce is also more transient in nature than it used to be, with less loyalty and shorter tenures. Some people call this a ‘skills gap’ that is growing and causing severe operational and maintenance challenges in certain areas of manufacturing. The oil and gas industry is further challenged by both political pressures and public opinion with a perception of being an “undesirable” industry; this aggravates the problem of both retaining and also attracting new talent.
The skills gap
Industries must adapt to the changing nature of the workforce. The traditional ways of doing things no longer works effectively. So how is the skills gap affecting the world of sulphur and what can be done to close it? Voovio has been collecting feedback from its customers, including major refining companies, and is hearing the same concerns everywhere:
- We are losing subject matter experts (SMEs) and ‘tribal knowledge.’
- As experts leave, they take their years of valuable and undocumented information and techniques with them decreasing the number of experts that a company can rely on.
- As experts leave, they take their years of valuable and undocumented information and techniques with them decreasing the number of experts that a company can rely on.
- The ‘Industrial SME’ is becoming a less-desirable career path for younger generations. Onboarding the traditional way does not work.
- Younger generations have grown up with less hands-on mechanical intuition – life is increasingly automated and technology-based.
- Traditional training cycles are significantly longer due to spending countless hours of classroom training with PowerPoint slides and training manuals, logging time shadowing or under the watchful eye of a mentor or looking up information in a manual.
- Often, validated training records (particularly refresher training) do not exist and are subject to OSHA violations.
- We rely on only a few SMEs for handson training.Training is usually people-dependent (highly variable) versus being system based and standardised. As mentioned above, fewer new SMEs are entering the workforce and therefore SME knowledge is not being effectively transferred.
- Operators have experienced 50% or less of what they need to know on qualification.
- In fact, some major petrochemical and refining facilities say it may be as low as 20-30%.
- Qualification time can be 3-6 months.
- Practice in the field does not match procedure.
- There is variability in how different shifts perform the same procedures or tasks in the field.
- Procedures are often generic or openended in nature, therefore execution and training is not standardised.
- This results in:
- Workers (SMEs) are overwhelmed;
- Unplanned events (equipment reliability);
- Near misses and incidents: safety, environmental, quality losses.
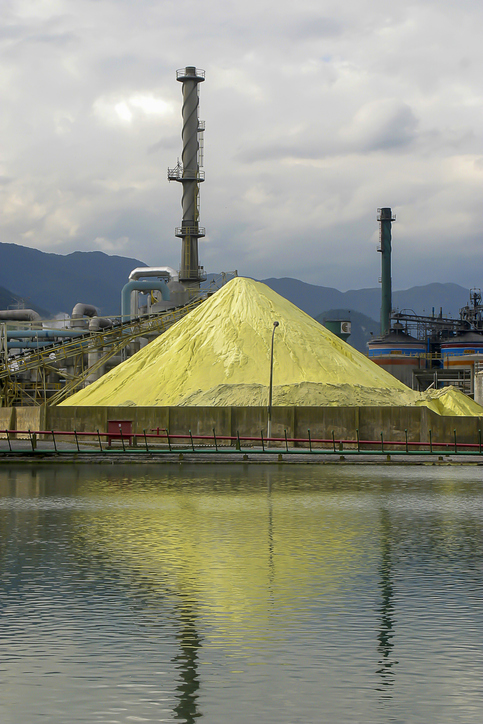
The skills gap in sulphur
Let’s look at some of the sulphur specific challenges that the sulphur industry is facing, and how we can solve them. The sulphur recovery unit (SRU) sits at the back end of the refinery or gas plant and is responsible for converting H2S from upstream units into elemental sulphur. While the SRU produces valuable steam from waste heat recovery, it is typically viewed as a cost centre due to historically low sulphur prices. This often leads to the misperception of the SRU as one of the less critical unit operations in the refinery or gas plant. To the contrary, stable, and reliable operation of the sulphur complex is vital for maximising onstream time of upstream unit operations; thus, although the SRU may not be a revenue generator, it can lead to lost production and revenue reduction for the entire facility if not operated smoothly. Most regions of the world require sulphur recovery efficiency in excess of 99.9%. As environmental regulations become more stringent, optimisation of the sulphur complex continues to be an operating challenge as the industry continues to approach near 100% sulphur recovery levels. In addition, today refiners deal with significant and frequent changes in crude slate which has a direct impact on the SRU operation. The challenge for operating companies is to keep the SRU online for a wide range of sulphur plant loads and to control emissions within regulatory limits, while minimising operating and maintenance costs. Although the process appears to be simple, H2S, SO2 and elemental sulphur have unique properties and problems do develop. Unexpected upsets and shutdowns of sulphur recovery operations can result in excess SO2 emissions and may increase plant maintenance costs due to corrosion and other damage.
Most operational challenges with SRUs occur during abnormal operation, such as feed disturbances from upstream amine and sour water stripping units, start-up, shutdown and/or turndown. The irony is that a well run sulphur recovery complex may have operators who are less prepared to deal with such abnormal conditions since they deal with them less frequently. This makes operator training, practice, and testing/qualification to deal with such conditions crucial for even the best run facilities in the world.
Another critical area that is often overlooked is utility systems. Specifically, the problems associated with the SRU utility systems have always existed, but it appears that in more recent years the frequency and severity of SRU problems associated with the utility systems have increased. It is suggested that the increase and severity of these problems are most likely related, but not limited, to the following items:
- Use of utilities may be intermittent;
- Utilities are not instrumented to the same degree as the primary process and even when they are instrumented, their maintenance is not prioritised as highly as process systems;
- DCS system has reduced field checkout; l high turnover/inexperienced operating staff;
- Overworked/understaffed operating and technical support staff;
- Lack of understanding of the intent and significance of all utility requirements.
By their nature some of the utility streams are used intermittently during start-ups, shutdowns and turndown operation. The industry has moved to lengthening the runtime between scheduled shutdowns. In the past, annual turnarounds were common, today scheduled turnarounds are typically three to four years apart. Several refineries are targeting five years between scheduled turnarounds. This change in turnaround philosophy has resulted in the start-up, shutdown and utility systems being less familiar to operating staff. It is also more likely that the operating staff has changed, and thus operating experience has been lost since the last turnaround. Furthermore, the extended runtime increases the possibility that the utility systems may have been compromised since the last usage.
Sulphur complexes appear to be relatively simple relative to most units in a refinery, however they can be very unforgiving if there is improper attention to detail. Successful operations place emphasis on cross training between process engineers, reliability improvement team members, maintenance personnel, and unit operators. The goal of the training should be to improve operational awareness and the important details in the SRU complex.
Knowledge automation solves a skills gap in sulphur recovery
Knowledge automation has been successfully deployed in the process industry and discrete manufacturing by BASF, SABIC, Halliburton, Tesla, Suncor, Linde, and many more, but what about sulphur? The following case study reviews how knowledge automation solved the skills gap in a sulphur recovery unit at a major US refinery.
The problem
Environmental incidents involving the planned or unplanned releases of substances from plant equipment can be environmentally harmful to air, water, and/or land. Incidents can also involve the breach of plant permits, complaints from local communities and environmental damage. Continued permit violations and regulatory exceedances can compromise a manufacturer’s “right to operate” resulting in suspension of operations.
The SRU at a major US refinery experienced several permit violations over a threeyear period in fines and expenses of over $500,000. These violations were largely attributed to human error due to the lack of operational knowledge with critical and/ or infrequent operating procedures. There were few SMEs who knew how to perform those procedures and the operators lacked the experience and training required (partly due to the high reliability of the unit, which reduced operator familiarity with start-ups and shutdowns).
The site team selected five highly critical and infrequent procedures, where knowledge gaps existed in the workforce and traditional training was not closing them. The procedures were chosen because a) they were not executed properly and/or followed, b) they are not adequate or clear, and/or c) a lack of operator experience exists. The five procedures were:
- Tail gas thermal oxidiser start-up;
- Shell Claus Off-gas Treater (SCOT) startup;
- SRU start-up;
- SCOT unit off-gas warmup bypass;
- Sour water system, gas to SRU.
The traditional training process:
- relies heavily on paper manuals;
- contains procedures with open-ended steps (general e.g. one step in the procedure might say ‘line up the pump’, which in reality may result in ten or more field actions);
- is very “person-dependent” (field training and manual evaluations) which results in ‘availability’ issues: SMEs need to be on shift and available to train.
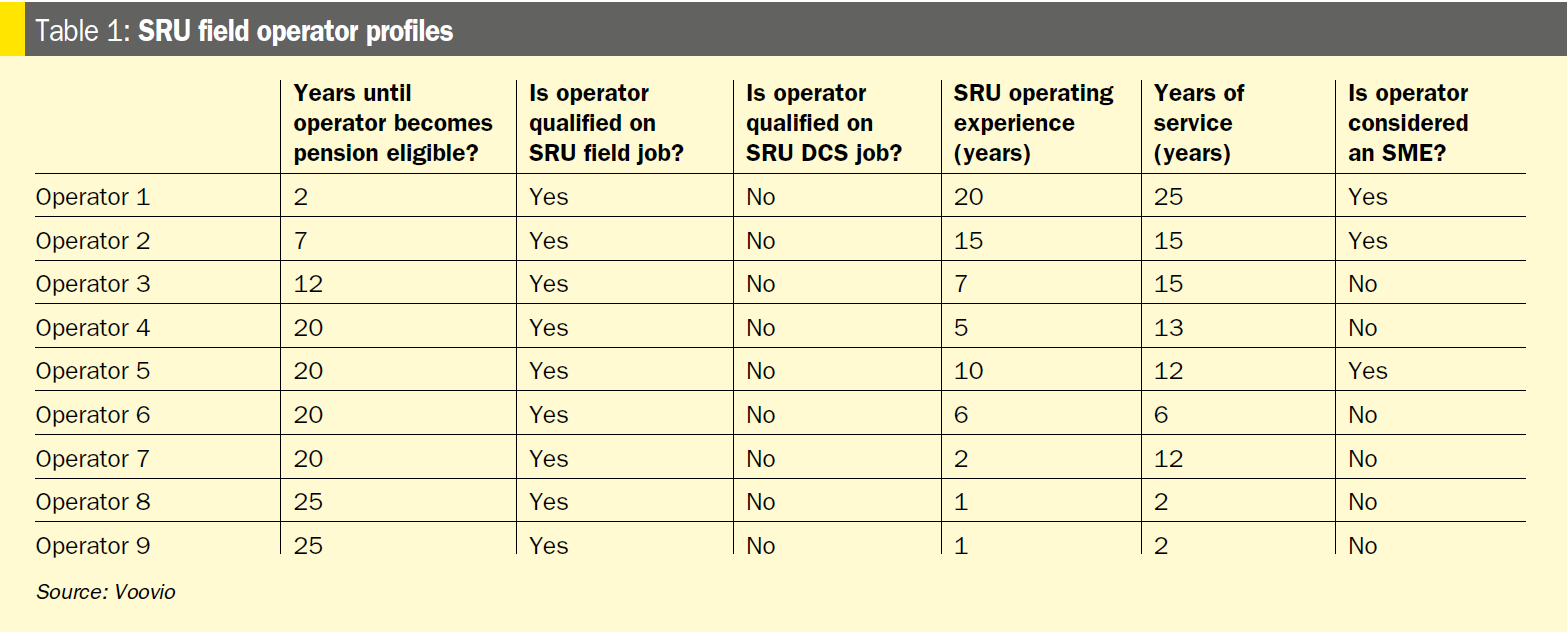
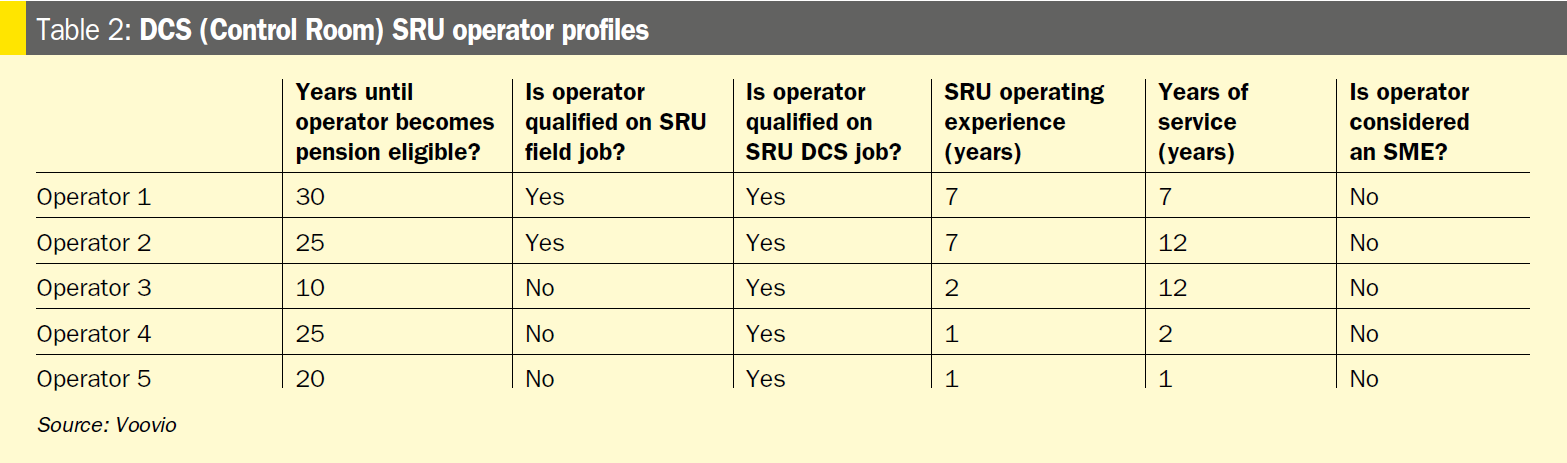
An SRU operators’ profile was developed (Tables 1 and 2) which illustrates that 2 out of 3 operators who were part of the SRU original start-up team were eligible for retirement very soon, taking critical undocumented knowledge with them and resulting in fewer/no experienced SMEs for training other operators.
The SRU field operator experience indicates that approximately 50% of the operators have more than six years of experience and probably have not experienced certain complex and/or intermittent tasks frequently enough to be fully competent. Three of five console operators have more than two years of experience. Most operators acknowledged that they have never experienced an actual full start-up.
The solution
The refinery chose to implement a knowledge automation platform that captured the critical undocumented SME knowledge (from the original SRU start-up team) within a digital replica and procedure simulators (see photos). This made this critical knowledge available 24/7 for all operators, allowing them to practice and review the procedures any time, thereby institutionalising and tandardising them. There was less reliance on SMEs and the simulation enhanced the scarce field training opportunities.
The digital replica (bottom image) provides a photorealistic immersive replica of the production unit, with all key components (valves, equipment) tagged and accessible in a searchable index. Operators can find things independently of an SME, available 24/7.
The simulation of flows (top image) allows operators to learn, review and even practice critical tasks such as valve line-ups in one real image. In Fig. 2 (procedure simulation) operators can learn, practice and test on procedures within the real digital replica environment of their production unit, accessible 24/7, allowing operators to review critical tasks when an SME or field training is not available.
Impact in the SRU
- Reduction in human error related to execution of these five procedures, leading to fewer environmental releases.
- Operators learned and demonstrated adequate knowledge of procedures 60-70% faster than traditional training methods.
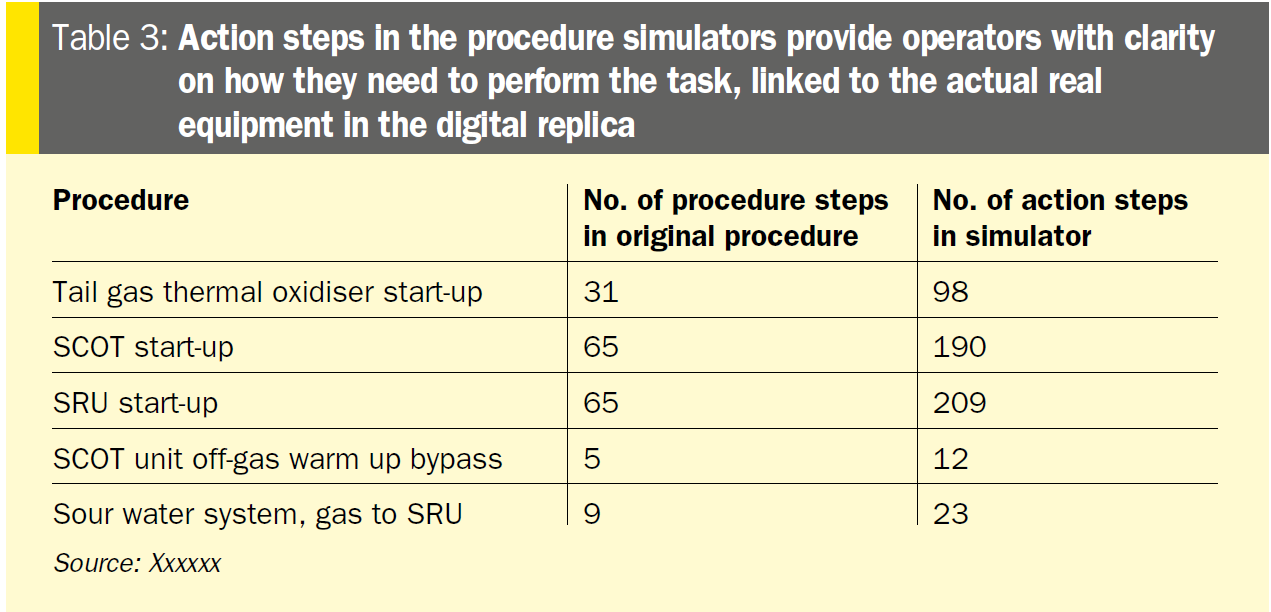
- Greater than 70% reduction of SME time dedicated to classroom and other training.
- Operators could access the simulators 24/7 without SME assistance – expertise was now available any time.
- Procedure clarity was achieved in the following ways:
- Clear, detailed action steps versus general instructions that are open ended (Table 3).
- Standardisation in the way people learn and review procedures (versus personal preference from one operator to the next).
In summary, the Voovio knowledge automation platform provides tools to standardise and maximise the effectiveness of an operator training and qualification program. This type of tool is essential for any type of manufacturing facility but has proven extremely useful in a sulphur recovery complex where an extensive knowledge gap existed. SRUs are critically important for maintaining overall facility onstream time, yet rarely get the credit they deserve due to their non-revenue-generating status. However, as knowledge is lost with retiring SMEs and other experienced operations staff, the importance of the SRU will be more widely exposed and implementation of knowledge automation tools will become non-negotiable.