WHITEPAPERS
Operation Errors: Procedure Clarity or Operator Execution?
It is well-documented that many manufacturing unplanned events could have been prevented if procedures were executed properly.
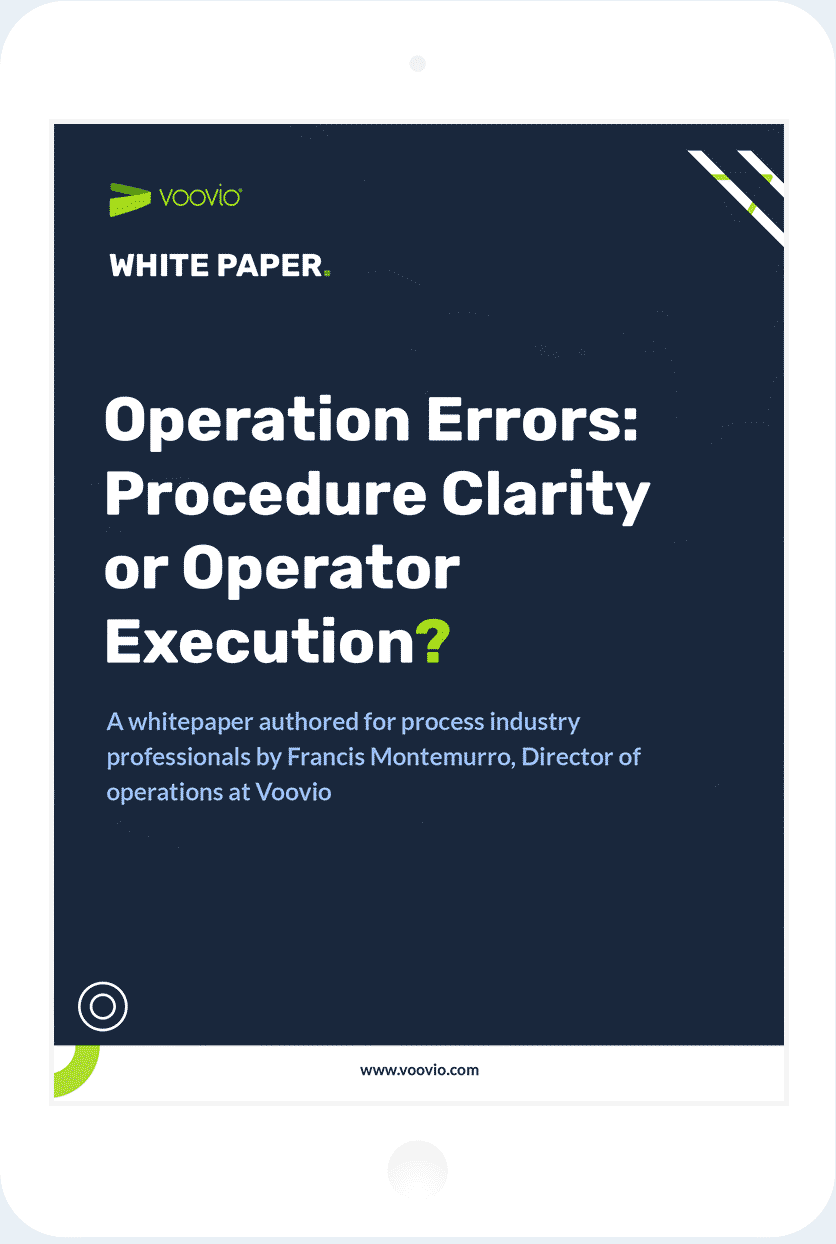
What’s Inside?
It is well-documented that many manufacturing unplanned events could have been prevented if procedures were executed properly. Ensuing investigations cite ‘failure to follow procedure’ as the event root cause resulting in next step recommendations, including additional operator training and discipline. However, we’ve collected data from across North America to understand the real reasons behind unplanned events.
In this white paper, Fran Montemurro (previously DuPont, now Director of Operations at Voovio) explores:
- Root causes for downtime
- Real-life examples from plants across North America
- Procedure quality best practice
….and much more. Download today to see how this might apply to your plant.
Who is it from?
This white paper was written by Francis Montemurro, Director of Operations at Voovio. With 30 years of experience in the manufacturing industry, Fran has extensive experience as a plant manager at multiple sites, highly hazardous PSM and EPA / RMP operations, as well as discrete manufacturing facilities. He was also awarded a Safety Excellence Medal & Engineering Excellence Award by DuPont – where he spent a large part of his career.
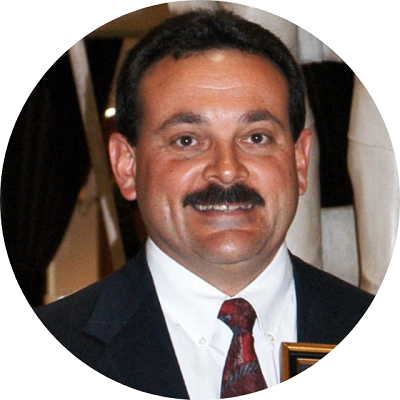
Table of contents
- Root causes for downtime
- Real-life examples from plants across North America
- Procedure quality best practice
- Root causes for downtime
- Real-life examples from plants across North America
- Procedure quality best practice